我國是*大的汽車產(chǎn)銷國之一,2011年汽 車產(chǎn)量接近產(chǎn)量的1/4。汽車噴涂作業(yè)是汽車 制造行業(yè)的關鍵污染環(huán)節(jié)。我國多數(shù)傳統(tǒng)汽車制造 企業(yè)仍在采用溶劑型涂料,其中的主要成分——有機 溶劑和稀釋劑不屬于成膜物質(zhì),*終均以大氣污染物 的形式進人環(huán)境。汽車行業(yè)排放的揮發(fā)性有機物 (VOCs) 包括苯系物、醇類、酯類、酮類等。國家大氣 污染防治相關規(guī)劃已明確提出,在重點區(qū)域新建排放 VOCs的項目應實行污染物排放減量替代, 實現(xiàn)增產(chǎn) 減污。就汽車涂裝行業(yè)而言,可從使用環(huán)保涂料、提 高工藝水平、優(yōu)化噴涂廢氣凈化技術等3方面著手, 實現(xiàn)VOCs的減排。 汽車噴涂VOCs產(chǎn)生環(huán)節(jié)及特征 傳統(tǒng)汽車涂裝工藝(采用溶劑漆)為:中涂一烘 干一底色漆一罩光漆(或兩道本色面漆)一烘干。在 噴涂工段,汽車車身依次進入噴漆室、流平室、烘干 室。每個工序均有VOCs排放, 噴漆室、流平室及烘 干室的VOCs產(chǎn)生量比例大致為60%、15%~25%和 25%~15%1 噴漆室廢氣主要污染物為未附著至工件表面的 漆霧和VOCs。多數(shù)企業(yè)采取水旋或其他濕式噴漆室 去除漆霧, VOCs去除效果十分有限。為保證工件質(zhì) 量,控制氣流不返混,噴漆室通常采用上進下排的氣流組織方式,斷面風速通常控制在0.25~0.5m/s,其 他工藝條件為:溫度22~27℃,濕度60%~80%。因 此,噴漆室廢氣的特點是廢氣量大、濕度大且含一定 的霧滴(其中漆霧不超過1mg/m*) 、VOCs濃度低(人 工噴涂段在100mg/m³以下,機器人段為100~ 200mg/m')。 流平室風速一般控制在0.1m/s以下,主要是保 證工件表面的成膜條件,其他參數(shù)與噴漆室相同。因 此, 流平室的主要污染物是VOCs, 濃度較噴漆室 略高。 烘干室廢氣的有機物(醇類、酯類、醚類、酮類、二 甲苯等)總濃度一般在2500mg/m左右,屬中高濃 度、高溫廢氣, 可采用燃燒法進行處理, 將VOCs轉(zhuǎn)化 為CO,和H,O121。 目前,在國內(nèi)汽車行業(yè),由于噴漆室、流平室廢氣 量大、VOCs濃度低, 絕大多數(shù)企業(yè)未采取處理措施, 而是直接通過幾十米高的排氣筒進行排放。也就是 說, 汽車噴涂行業(yè)約70%的VOCs均未經(jīng)處理直接進 人大氣環(huán)境。 2 汽車噴涂VOCs減排途徑 2.1 使用環(huán)保型涂料 汽車涂料主要有溶劑型、水性、粉末涂料3種類 型。溶劑型涂料的溶劑以甲苯、二甲苯、酯、醇、醚、酮 為主,溶劑占涂料的比重一般在40%~60%,*終均 以VOCs的形式進人環(huán)境。水性涂料的溶劑以水為 主,而有機溶劑含量較低,約占涂料比重的5%~ 15%。粉末涂料顧名思義為粉末狀涂料,由聚合物、顏料和添加劑組成,噴涂過程過噴的涂料可回收再利 用, 在成膜過程中VOCs產(chǎn)生量極少。一般來講, 同 等面積、同等厚度的涂層, 使用水性涂料的VOCs排 放量較使用溶劑型涂料可降低約70%,使用粉末涂 料排放的VOCs量大大低于水性涂料。 以國內(nèi)某大型合資汽車生產(chǎn)企業(yè)為例,2005年 建成投產(chǎn)的原涂裝車間采用三涂層涂裝工藝,均為溶 劑型涂料。污染源監(jiān)測表明,其噴漆室非甲烷總烴 (由于我國尚未頒布全國性的VOCs排放標準, 僅部 分省頒布了地方性排放標準,故國內(nèi)汽車行業(yè)仍普遍 以監(jiān)測非甲烷總烴來表征廢氣中揮發(fā)性有機物的排 放)產(chǎn)生量為42kg/h,其中二甲苯為38kg/h。而 2011年建成投產(chǎn)的新涂裝車間也采用三涂層工藝, 中涂和底色漆采用水性涂料,罩光漆采用溶劑型涂 料,且兩個車間產(chǎn)能相同。污染源監(jiān)測表明,新涂裝 車間噴漆室非甲烷總烴產(chǎn)生量為26kg/h,其中二甲 苯為8kg/h。使用水性涂裝工藝后,非甲烷總烴減少 了40%,二甲苯減少了近79%。 使用溶劑型涂料,一輛涂裝面積為80m²的普 通轎車的VOC產(chǎn)生量在10kg左右, 平均為 125g/m²01.歐盟規(guī)定,新建汽車涂裝車間車身單 位面積VOCs產(chǎn)生量不高于45g/m; 德國標準為不 高于35g/m;我國《清潔生產(chǎn)標準汽車制造業(yè)(涂 裝) 》(HJ/T 293―2006) 提出的VOCs產(chǎn)生指標如 表1所示。
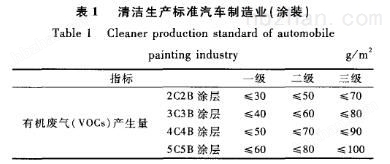
近幾年,歐盟國家新建生產(chǎn)線全部采用水性中涂 和水性底色漆,罩光漆已開始采用水性清漆和粉末清 漆,個別生產(chǎn)線全部采用粉末涂裝。在北美,新建生 產(chǎn)線主要使用水性中涂或粉末中涂,底色漆使用水性 漆41。在國內(nèi),近10年新建汽車生產(chǎn)線總體上均采 用水性中涂和水性底色漆,罩光漆仍采用溶劑型漆, 整車涂裝尚無使用粉末型涂料的案例。因此,與歐盟 和北美區(qū)域的一些國家相比,我國汽車行業(yè)涂料的整 體環(huán)保水平仍有待提高。
就水性涂料而言,使用成本高、涂刷要求高、生產(chǎn) 改造難度大,是阻礙其在汽車涂裝行業(yè)廣泛推廣的3 大原因。就粉末涂料而言,汽車粉末涂料不能像液體 涂料那樣可以迅速換色,雖物理和化學性能很好,但 涂層外觀平整性、光滑性和光澤等尚不能與溶劑型涂 料相媲美,造成粉末涂料難以推廣。國外公司研究起 步較早,粉末涂料已廣泛用于底漆噴涂;在面漆噴涂 方面, 一種基于GMA(甲基丙烯酸縮水甘油酯) 、用脂 肪酸或酸酐固化的丙烯酸粉末涂料已在美國某汽車 生產(chǎn)線中投人使用,將其噴涂在車身表面后具有異常 平整的涂膜外觀和優(yōu)良的耐久性,已接近汽車面 漆要求。隨著我國對VOCs等大氣污染物重視程 度的提升,汽車行業(yè)涂料環(huán)?;潜亟?jīng)之路,各企業(yè) 必須積極改進汽車用涂料,以期實現(xiàn)整個行業(yè)的 VOCs減排。 2.2 提高噴涂工藝水平 涂裝工藝水平?jīng)Q定涂料的有效利用水平。涂裝 工藝*,涂料利用率高,則過噴漆霧少、廢氣污染 物排放量??;反之,則過噴漆霧量大、廢氣污染物排 放量大。汽車涂裝企業(yè)如果采用機械人自動仿形、 靜電旋杯噴涂,則出漆量及噴涂圖形可根據(jù)車身的 不同位置調(diào)整到*佳狀態(tài)。采用大容量低壓噴槍、 無氣噴槍等*噴槍,可使涂料利用率提高到 70%,甚至90%以上,物料流失率低,廢氣污染物排 放量大大減少(o。另外,在確保涂裝質(zhì)量不顯著改變的前提下,通 過調(diào)整和簡化涂裝工藝,將大大節(jié)省資源、能源消耗, 同時減少VOCs排放。傳統(tǒng)涂裝工藝一般為3C2B, 包括中涂一烘干一底色漆一罩光漆一烘干幾個主要 步驟。目前,在傳統(tǒng)工藝的基礎上,先后出現(xiàn)了日本 馬自達公司的3C1B涂裝工藝、杜邦公司的2C1B涂 裝工藝、BASF公司的雙底色工藝等。具體介紹如下: (1)3C1B工藝即在3C2B工藝基礎上取消中涂 烘干工序,其總涂層(磷化膜+電泳膜+中涂+底色 漆+清漆)厚度為76~92um,較3C2B工藝減少了約 10um, 在降低成本的同時, 減少VOCs排放量達45% 以上[a。 (2)2C1B工藝即二涂層工藝,通過取消中涂噴漆 和中涂烘干工序,改善底漆和面漆的機械性能、耐候 性能和表面裝飾性能,達到“三涂層涂裝工藝”的功 能。2C1B工藝的總涂層厚度為69~85jm,較3C2B工藝減少了約17um,進一步降低了成本、減少了 VOCs排放量。 (3)雙底色漆涂裝工藝是將正常的中涂層取消, 將原來的一道底色漆設計為兩涂層,為了達到和正常 工藝相同的耐候性能,在底色漆中加人吸收紫外線的 組分,在罩光漆中加人抗紫外線的組分。采用雙底色 漆涂裝工藝的VOCs排放量較傳統(tǒng)工藝可減少30% 以上a1。 綜上所述,涂裝工藝的改進可從采用全自動噴 涂、采用靜電旋杯噴涂、簡化涂裝工藝等方面著手,由 于降低了過噴漆霧和涂層厚度,可大大減少噴涂作業(yè) 中VOCs的產(chǎn)生量, 達到減排目的。目前, 國內(nèi)主要 有南京福自達涂裝線采用3C1B工藝,一汽大眾 成都三廠涂裝線采用2C1B工藝。但總體來看,國內(nèi) 采用簡化涂裝工藝的汽車廠家還不夠普及。
2.3 優(yōu)化噴涂廢氣治理技術 汽車噴涂行業(yè)的VOCs排放源點主要包括噴漆 室廢氣、流平室廢氣、烘干室廢氣等。國內(nèi)汽車行業(yè) 從降低成本角度考慮,絕大多數(shù)企業(yè)將噴漆室廢氣、 流平室廢氣統(tǒng)一收集后直接排放, 而未對VOCs進行 有效處理。其噴漆室廢氣實際上屬于稀釋排放,一條 大型車身涂裝線每年排放的VOCs總量可能高達數(shù) 百噸,對大氣造成的危害非常嚴重。對于烘干室廢 氣, 普遍采取燃燒處理, 治理方法有催化燃燒法(CIU 法) 、回收式熱力燃燒法(TAR法) 和蓄熱式熱力燃燒 法(R TO法) 等”, 對烘干廢氣中VOCs的去除率達 95%~99%,并且有的方法還可實現(xiàn)廢熱回收利用。 因此, 烘干室廢氣*終進人大氣的VOCs排放量遠遠 低于噴漆室廢氣,不足噴漆室廢氣的1%。 在國內(nèi)汽車涂裝行業(yè)尚不能*采用環(huán)保型水 性涂料或粉末涂料的狀況下,要大幅度降低噴涂環(huán)節(jié)的VOCs排放量, 應逐步加大環(huán)保投人, 引進技術或自主研發(fā)*方法,對噴漆室、流平室廢氣 進行有效處理,而不是直接排放。借鑒國外涂裝企業(yè) 對噴漆室和流平室廢氣的處理經(jīng)驗,可采用吸附法處 理,即先利用吸附材料(如活性炭、沸石)將氣體或蒸 汽吸附在其表面,隨后進行熱解吸,使有機廢氣濃縮 10~15倍,再對濃縮廢氣采用催化燃燒或蓄熱式熱 力燃燒的方法進行處理。
目前, 我國已經(jīng)明確了VOCs減排目標, 針對汽 車噴涂行業(yè),應推廣使用環(huán)保性涂料(如水性涂料和 粉末型涂料)、改進噴涂工藝,降低有機溶劑的使用 量。需要特別注意的是,考慮成本問題,我國汽車涂 裝行業(yè)絕大多數(shù)企業(yè)均未對噴漆室廢氣和流平室廢 氣進行*處理,而是直接排放,建議借鑒 治理經(jīng)驗,逐步試行噴漆廢氣的濃縮、燃燒處理技術, 大力削減該行業(yè)VOCs排放水平。